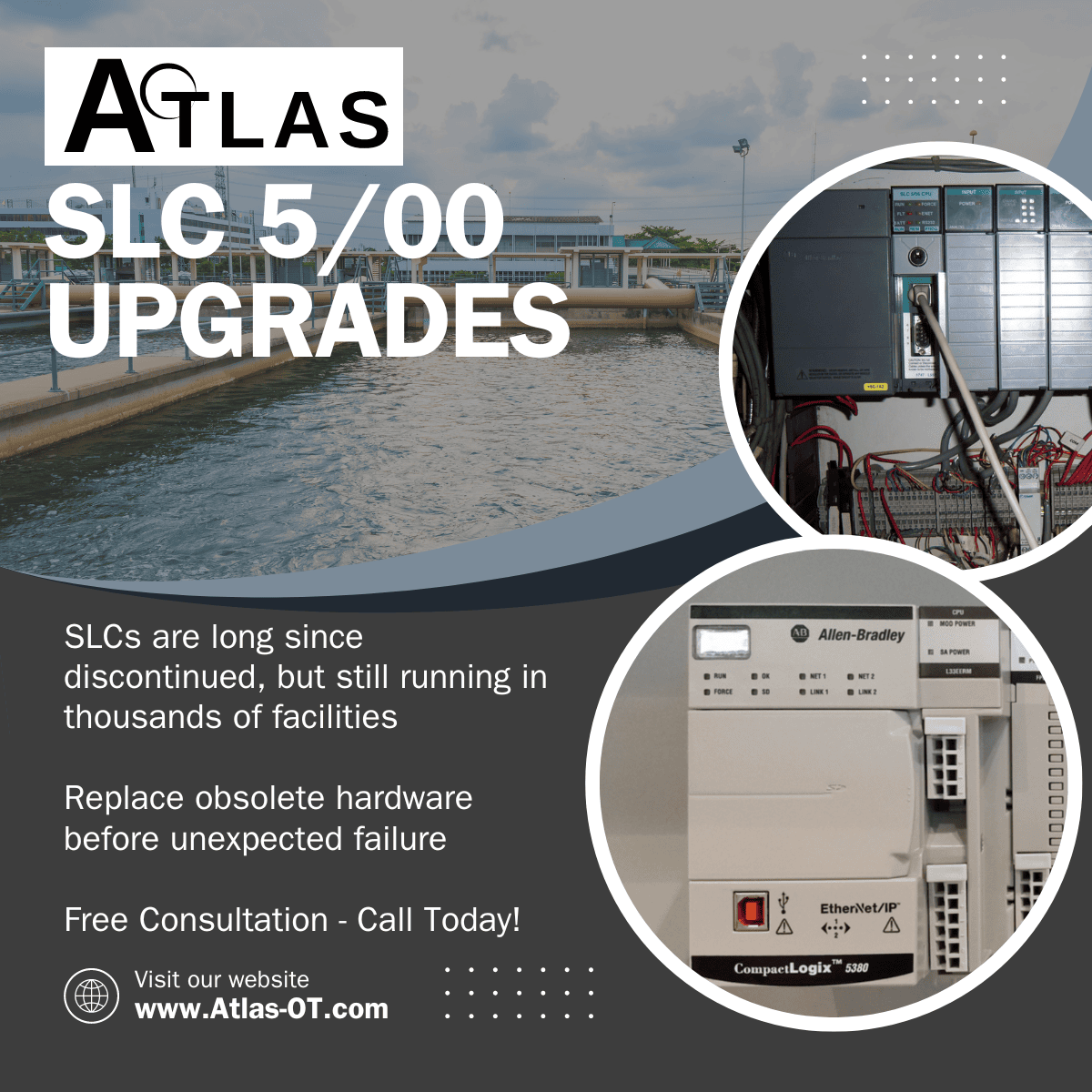
Why Replace Your SLC 500 PLC?
Why Replace Your SLC 500 PLC?
As industrial automation technology continues to advance, many manufacturers find themselves at a crossroads with their legacy control systems. The Rockwell SLC 500 PLC, a workhorse in the industry for decades, is now reaching the end of its lifecycle. This article explores the reasons for upgrading and provides guidance on how to approach the replacement process.
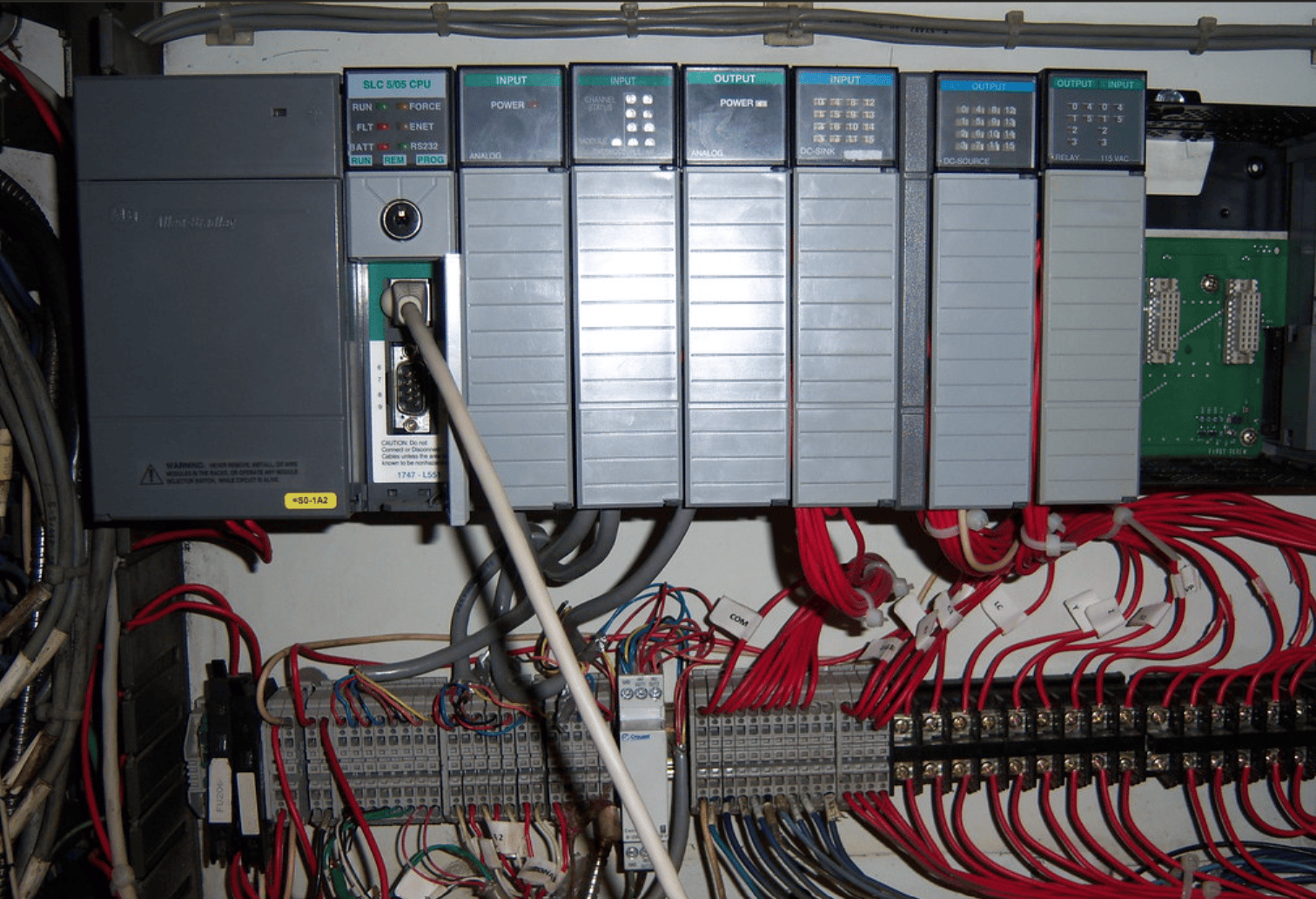
Obsolescence and Support Concerns
Obsolescence and Support Concerns
- Difficulty in obtaining replacement parts
- Lack of technical support
- Increased downtime due to aging hardware
Processing Power and Memory Constraints
Processing Power and Memory Constraints
SLC 500 processors have limited computational capabilities compared to modern PLCs. This restriction becomes particularly apparent when dealing with complex control algorithms or large amounts of data processing. The SLC 500's memory capacity is also relatively small, which can hinder the implementation of more sophisticated control strategies or the storage of extensive historical data.
Communication Bottlenecks
Communication Bottlenecks
The communication options available on SLC 500 PLCs are limited and often slower than modern standards. While some models offer Ethernet connectivity, the data transfer rates and protocols supported are not on par with current industrial networking requirements. This limitation can create bottlenecks in data exchange between the PLC and other systems, impacting real-time control and monitoring capabilities.
Synchronous I/O Scanning
Synchronous I/O Scanning
SLC 500 processors use a synchronous I/O scanning method, where input and output data is updated in sync with the program scan. While this ensures data consistency throughout a scan cycle, it can lead to longer overall scan times and reduced responsiveness in high-speed applications. Modern PLCs often use asynchronous I/O scanning, which can provide more flexibility and improved performance in certain scenarios.
Enhanced Features of Modern PLC Systems
Enhanced Features of Modern PLC Systems
Modern PLC systems, such as the CompactLogix 5380, offer numerous advanced features that address the limitations of legacy systems and provide additional capabilities.
Increased Processing Power and Memory
Increased Processing Power and Memory
Contemporary PLCs boast significantly higher processing speeds and larger memory capacities. This enhancement allows for more complex control algorithms, faster execution times, and the ability to handle larger data sets. For instance, users can expect a decrease of 50-80% in overall program scan time when migrating from an SLC 500 to a Logix-based controller.
Advanced Communication Capabilities
Advanced Communication Capabilities
Modern PLCs support a wide range of communication protocols and offer high-speed Ethernet connectivity. This improved communication infrastructure enables seamless integration with other systems, supports Industrial Internet of Things (IIoT) applications, and facilitates real-time data exchange. The CompactLogix 5380, for example, offers integrated motion control on EtherNet/IP, providing increased flexibility and performance.
Enhanced Security Features
Enhanced Security Features
With cybersecurity becoming increasingly critical in industrial environments, modern PLCs incorporate advanced security measures. These include regular security updates, compliance with current cybersecurity standards, and features like secure boot and encrypted firmware. Such enhancements significantly reduce the risk of cyber attacks and unauthorized access.
Improved Diagnostics and Maintenance
Improved Diagnostics and Maintenance
Contemporary PLC systems offer sophisticated diagnostic capabilities and predictive maintenance features. These allow operators to identify and address potential issues before they lead to system failures. Real-time diagnostics and remote monitoring capabilities contribute to reduced downtime and improved overall system reliability.
Scalability and Flexibility
Scalability and Flexibility
Modern PLC platforms are designed with scalability in mind. They often support modular architectures that allow for easy expansion of I/O and processing capabilities. This flexibility enables users to adapt their control systems to changing requirements without the need for complete system overhauls.
Integrated Development Environments
Integrated Development Environments
PLCs like the CompactLogix 5380 utilize advanced programming software that offers a common development environment across different controller types. This integration streamlines the programming process, reduces commissioning time, and allows for more efficient code reuse and management.
How to Approach the Replacement Process
How to Approach the Replacement Process
1. Assess Your Current System
- Inventory all hardware components
- Document I/O configurations
- Review and catalog all programming logic
2. Define Future Requirements
- Evaluate potential increases in I/O count
- Assess communication needs with other systems
- Consider integration with SCADA or other higher-level systems
3. Choose the Right Replacement
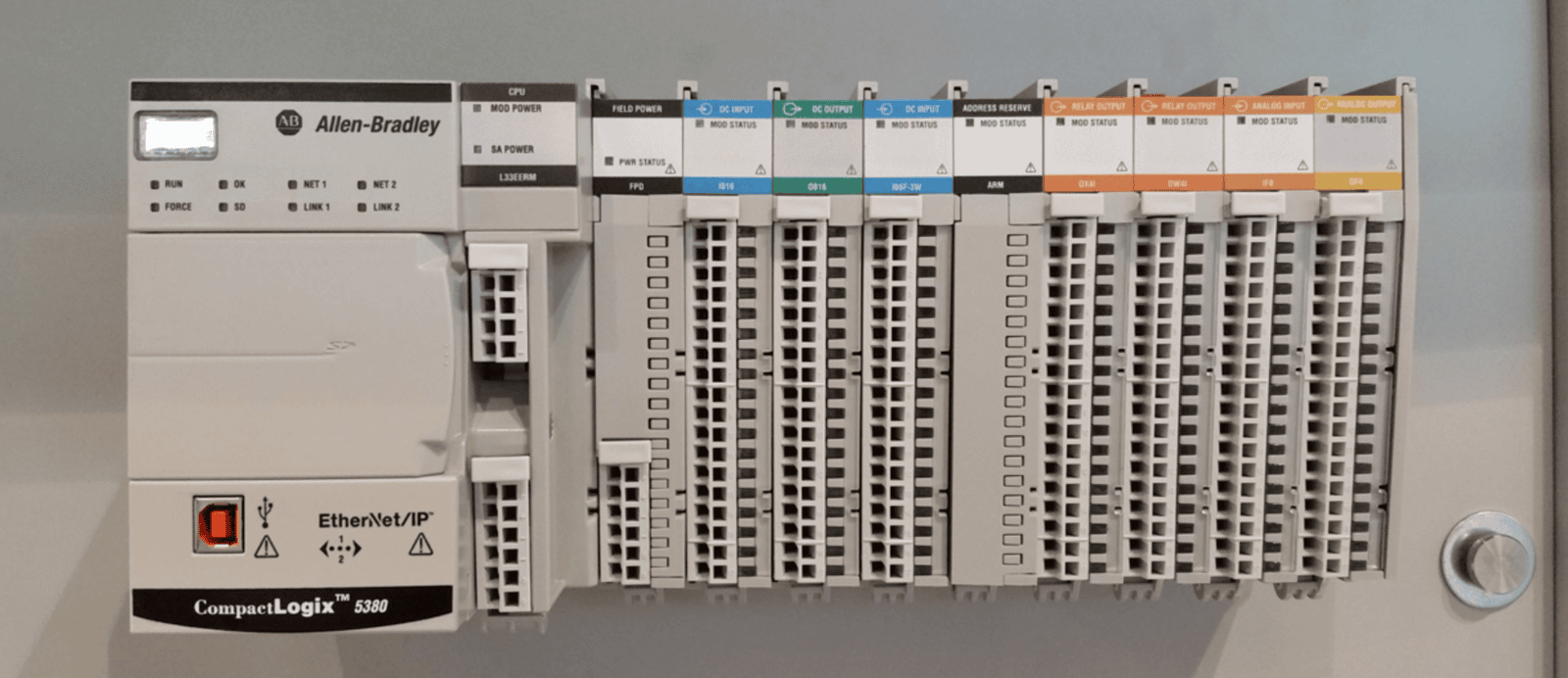
- Compatibility with existing infrastructure
- Scalability for future expansion
- A common development environment for reduced commissioning time
4. Plan the Migration Strategy
- Complete system replacement
- Phased migration, potentially retaining some existing I/O
- Hot cutover to minimize production downtime
5. Utilize Available Tools and Resources
- Integrated Architecture Builder (IAB) for hardware migration planning
- Studio 5000 Logix Designer for programming
- Conversion tools for translating SLC ladder logic to Logix
6. Consider Professional Assistance
- Rockwell Automation Conversion and Migration Services
- Certified system integrators with experience in SLC to CompactLogix migrations - Like Atlas OT